Człowiek oddycha przeciętnie 16 milionów razy w ciągu dwóch lat. Tyle właśnie wytrzymać musi stalowy implant wszczepiany przy operacjach korygujących deformacje klatki piersiowej. Dzięki innowacyjnemu stanowisku testowemu stworzonemu przez badaczy z Łukasiewicz – Poznańskiego Instytutu Technologicznego, proces ten skrócono do zaledwie miesiąca. A to tylko jedna z kilku nowości, które znacząco poprawią komfort życia osób cierpiących na tzw. klatkę lejkowatą i kurzą.
Implant, który oddycha jak człowiek
Lejkowata i kurza klatka piersiowa to deformacje, które dotykają dzieci i dorosłych, powodując nie tylko dyskomfort estetyczny, ale i realne problemy zdrowotne. Wada lejkowata wiąże się z zapadnięciem dolnej części mostka, co w zaawansowanych przypadkach prowadzi do ucisku na serce i płuca, zmniejszenia pojemności oddechowej, zaburzeń krążenia i duszności. Z kolei kurza klatka piersiowa, w której mostek i żebra odstają do przodu, ogranicza ruchomość i również może utrudniać oddychanie.
Czytaj też: Nowatorski zabieg wszczepienia hydraulicznego implantu prącia w Warszawie
Najskuteczniejszą metodą leczenia obu deformacji jest chirurgiczna implantacja specjalnie wygiętej, podłużnej płytki ze stali nierdzewnej, która – po dwóch latach noszenia – koryguje pozycję mostka i żeber.
Dotychczas stosowane implanty były mocowane przy użyciu drutów, które przebijały żebra – zabieg skuteczny, ale bolesny, niosący ryzyko uszkodzeń tkanek i konieczność długiej rekonwalescencji. Odpowiedzią na te problemy jest nowy typ implantu opracowany przez konsorcjum naukowo-przemysłowe: firmę BHH Mikromed, Akademię Górniczo-Hutniczą, Łukasiewicz – PIT oraz Klinikę Chirurgii Wad Rozwojowych Dzieci i Traumatologii Śląskiego Uniwersytetu Medycznego w Zabrzu.
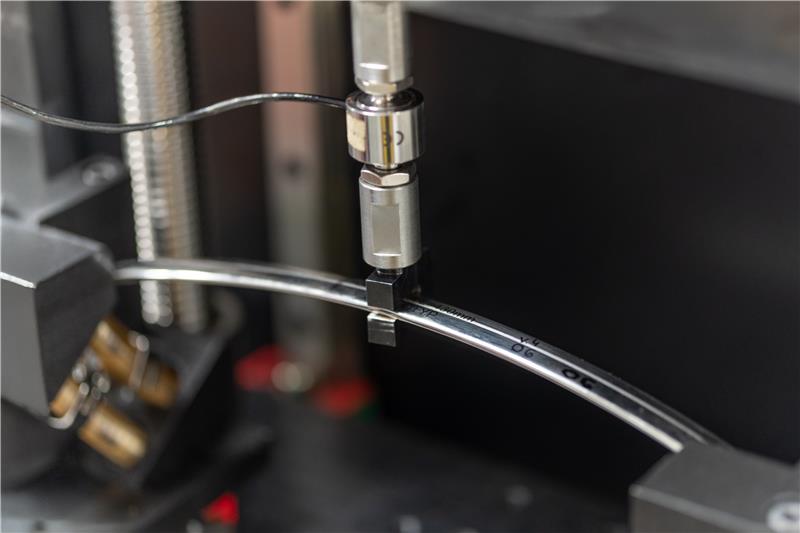
Zamiast drutu, zastosowano tzw. „łapki” ze stali nierdzewnej, które mocują się do żeber bez konieczności ich nawiercania. Dzięki temu implant jest bardziej stabilny, mniej inwazyjny i komfortowy dla pacjenta.
Zanim jednak implant trafi na salę operacyjną, musi przejść rygorystyczne testy mechaniczne. Badacze z Łukasiewicz – PIT stworzyli specjalne stanowisko badawcze, które odtwarza warunki pracy ludzkiej klatki piersiowej podczas oddychania. Implanty, umieszczone na wydrukowanych w 3D sztucznych żebrach, poddawane są siłom odpowiadającym naturalnym naciskom i odkształceniom.
Dr inż. Joanna Sulej-Chojnacka z Łukasiewicz – PIT mówi:
Sprawdzamy, jak się zachowuje ten materiał: czy nie pęka, czy jego powierzchnia się nie zmienia, czy się nie wysuwa z żeber, czy śruby implantów wciąż mocno trzymają. W ciągu miesiąca poddajemy implant 16 milionom nacisków, co odpowiada liczbie wdechów i wydechów, jaką człowiek robi przez dwa lata. Po tych testach zmęczeniowych analizujemy jeszcze każdy implant pod mikroskopem, by wychwycić niewidoczne gołym okiem zmiany.
Testowanych jest aż dziesięć różnych rozmiarów implantów, aby jak najlepiej dopasować je do anatomii różnych pacjentów.
Zakończenie testów zaplanowano na koniec bieżącego roku. Jeżeli wszystko przebiegnie pomyślnie, nowe implanty mogą trafić do użytku klinicznego już w 2026 roku. Dla pacjentów z wadami klatki piersiowej to szansa na szybszy powrót do zdrowia, mniejsze dolegliwości bólowe i znacznie wyższy komfort życia po operacji.